One thing is almost always constant in business: Risk. All industries have diverse levels of risk. Some industries are riskier than others. Especially managing risk management in the EHS Industry.
- Risk to the financial wellbeing of an operation
- Risk to the environment because of an unannounced spill
- Risk to a chemical process that disrupts the final product
- Then we have the most important risk to consider; workers getting hurt.
According to the recent numbers from the National Safety Council (Most Dangerous Industries – Injury Facts) here are the top five industries that had the highest risk.
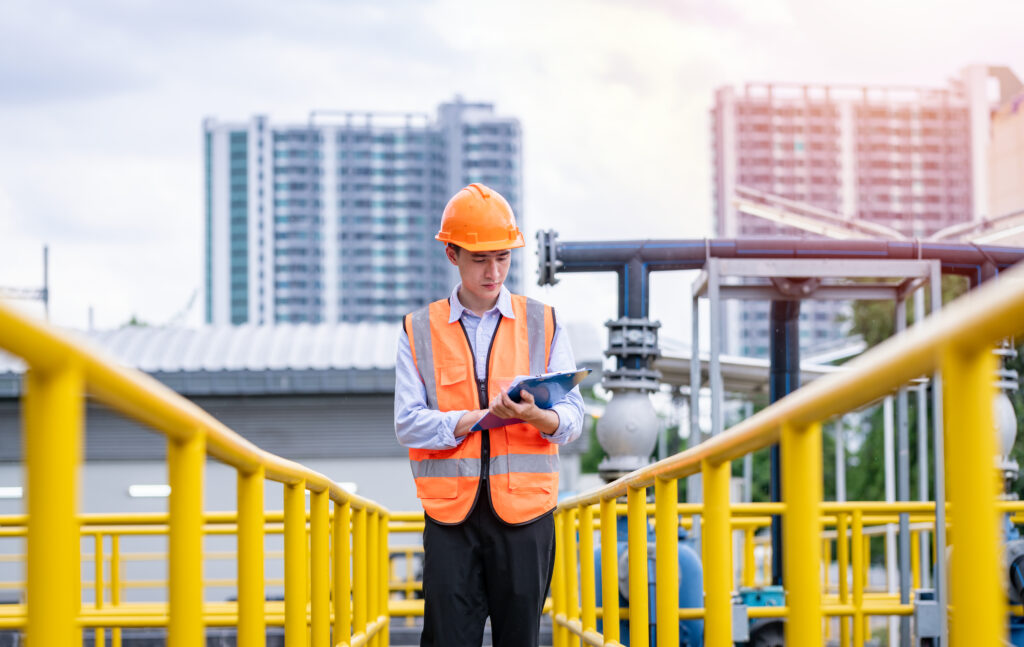
Most Dangerous Industries
When exploring work-related injury, illness, and fatality trends, the question “What is the most dangerous industry?” often comes up. Because work-related “danger” is defined in several diverse ways, there is no one answer to this seemingly simple question.
In 2022, depending on the measure used, each of these four industries could be ranked as most dangerous:
- Construction– experienced the most workplace deaths.
- Education and health services– experienced the most nonfatal injuries and illnesses involving days away from work.
- Agriculture, forestry, fishing, and hunting– experienced the highest death rate per 100,000 workers.
- Transportation and warehousing– experienced the highest injury and illness rate involving days away from work per 10,000 workers.
Agriculture, forestry, fishing, and hunting
- Fatality rate per 100,00 workers: 18.6
- Number of fatalities: 417
- Nonfatal injury and illnesses involving days away from work rate per 10,000 workers: 160
- Number of nonfatal injury and illnesses involving days away from work: 15,200
Mining
- Fatality rate per 100,00 workers: 16.6
- Number of fatalities: 113
- Nonfatal injury and illnesses involving days away from work rate per 10,000 workers: 70
- Number of nonfatal injury and illnesses involving days away from work: 4,100
Transportation and warehousing
- Fatality rate per 100,00 workers: 14.1
- Number of fatalities: 1053
- Nonfatal injury and illnesses involving days away from work rate per 10,000 workers: 220
- Number of nonfatal injury and illnesses involving days away from work: 129,500
Construction
- Fatality rate per 100,00 workers: 9.6
- Number of fatalities: 1069
- Nonfatal injury and illnesses involving days away from work rate per 10,000 workers: 100
- Number of nonfatal injury and illnesses involving days away from work: 71,700
Wholesale trade
- Fatality rate per 100,00 workers: 5.4
- Number of fatalities: 171
- Nonfatal injury and illnesses involving days away from work rate per 10,000 workers: 110
- Number of nonfatal injury and illnesses involving days away from work: 62,200
So, what do the numbers tell us? That risk is a constant factor in the workplace. Especially risk management in the EHS Industry.
Organizational plans should include methods to reduce risk. When it comes to workplace risks, a person who can identify those risks as well as the potential losses must be a major part of that organizational plan.
What attributes will that person possess to identity those risks and hazards and reduce the potential outcome?
A nationally recognized construction research group, CPWR (The Center for Construction Research and Training | www.cpwr.com), provided us with a solution.
Foundations for Safety Leadership (FSL) Training Course
The Foundations for Safety Leadership (FSL) training program was completed in the spring of 2016 and on January 1, 2017, OSHA’s Directorate of Training and Education approved it as an official elective in their construction 30-hour course.
The 2.5-hour Foundations for Safety Leadership (FSL) is a highly interactive training program that teaches foremen, supervisors, and other front-line leaders on construction job sites about the costs of ineffective, and the benefits of effective safety leadership such as improved safety climate and reduced negative safety outcomes.
Most importantly, it includes information on critical leadership skills to use on the job site and presents students with different safety scenarios which they review and then decide which leadership skills would help address the specific worksite hazard.
Since its roll-out in January 2017, about one million individuals have taken the FSL either during the 30-hour course or as part of a company or union training program. As a testament to its popularity, it has been or is currently being adapted for the U.S. Department of Energy and the oil and gas industry.
The focus of the training program is to teach the five skills and actions of an effective safety leader.
Each skill is divided into a leadership skill set with a good leadership action outcome.
First Skill
Leads by Example
Outcomes: Establishes safety expectations as a core value.
- Shares safety vision with team members
- Demonstrates a positive attitude about safety
- “Walks the Talk”
- Leads Up!
Second Skill
Engages and Empowers Team Members
Outcomes: Engages, encourages, and empowers team members to identify and act upon unsafe conditions by…
- Reporting hazards and safety concerns
- Providing solutions
- Reporting near misses (good catches)
- Stopping work if necessary
Third Skill
Actively Listens and Practices 3-Way
Outcomes: Actively listens to hear what team members are saying
- Practices 3-way communication by having person repeat the message they heard
Fourth Skill
Develops Team Members Through Teaching, Coaching, and Feedback
Outcomes: Respectfully teaches and coaches workers
- Watches the learner fix the hazardous situation or perform the task to make sure it’s done correctly
- Focuses on potential consequences rather than on the team member
- Uses the FIST principle: Facts, Impact, Suggestions, Timely
Fifth Skill
Recognizes Team Members for a Job Well Done
Outcomes: Privately and/or publicly acknowledges team members for going above and beyond when it comes to safety
We often ask how organizations get to be really good at safety. The answer is that they first became great at training and education. Set a goal of not only becoming great at safety but maintaining it. Develop organizational training and education for safety with a focus on the actions that address either our understanding or mitigation of risk.
Moving safety forward does not mean changes are going to happen immediately. It begins with accomplishing small but important goals that set the stage for what comes next. The key is to think long term. Focus on gains that better position your organization to meet challenges now and in the future.
You don’t have to carry the weight of risk management in the EHS industry alone. Whether you’re navigating regulatory demands, scaling your team, or responding to changing job site conditions, ResponsAble Safety Staffing is here to help. Our experienced safety professionals are ready to step in with the training, certifications, and mindset needed to keep your workforce safe and compliant.
Ready to strengthen your safety strategy?
👉 Contact our team today or learn more about our staffing services to see how we can support your business.