A New Year is always time to rethink and recharge your goals and ambitions.
A fresh start to so many things. What about your safety culture and the supervisors and workers that are a part of it? It’s time to enhance your safety culture in 2025!
Consider the following recommendations enhancing safety culture in 2025.
Enhancing Safety Culture in 2025
Rebranding
Create a new safety slogan for 2025. Make it a team effort and involve everyone in the organization. Have a slogan that represents a fresh start to a New Year with many opportunities to improve the safety culture.
Branding your safety and health programs can produce many desirable and profitable results.
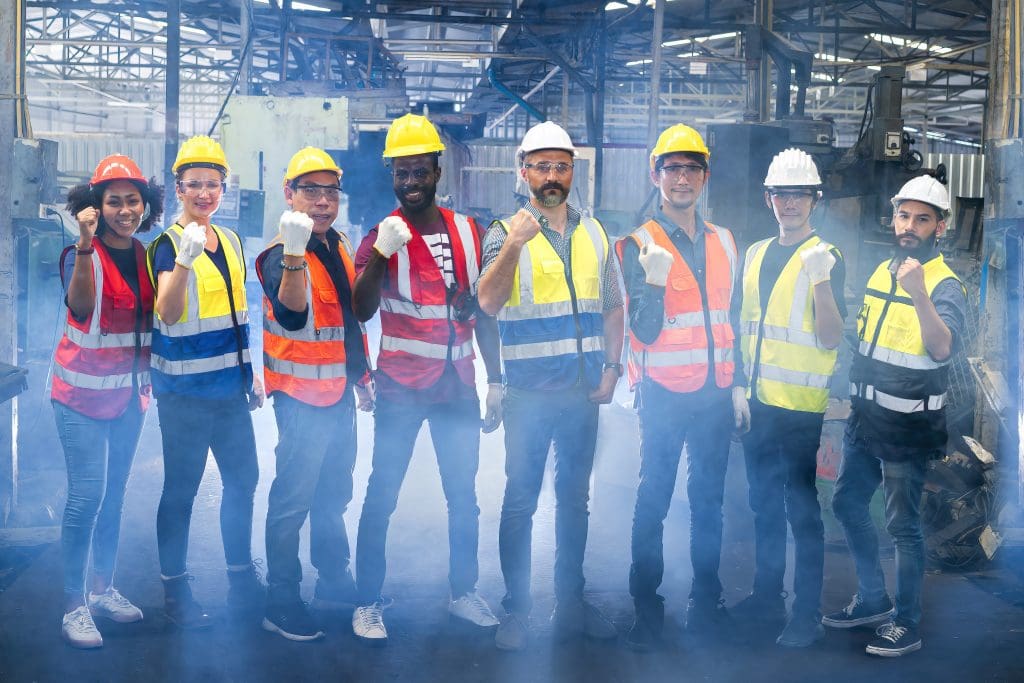
Support a Safety Committee
Engage a safety committee to guide the organization into the new year with fresh ideas and new endeavors. Safety committees can be a launching pad for valuable new and innovative ideas to improve the organization’s safety and health programs.
Safety committees should include at least three and not more than five committee members. Two of the committee members should have safety and health responsibilities. A third member should be a non-supervisory worker who will be temporary and replaced by invitation on a suggested three-month basis.
The committee’s goal will be to advise the employer regarding safety in the workplace, including suggestions from employees regarding safety conditions in the workplace: to receive employee notifications of workplace safety conditions and to develop procedures by which an employee can notify the committee of workplace safety conditions.
For more information, read: Safety_and_Health_Programs_in_the_States_White_Paper.pdf
Update the Training
Create a training plan and matrix for everyone, from upper management to frontline workers. Review the organization’s NAICS code and develop the OSHA required training to match your code. Learn more about your organization’s NAICS code here: North American Industry Classification System (NAICS) U.S. Census Bureau
Select an employee to become the go to trainer in the organization. The OSHA Outreach Training Program is an excellent starting point. To learn more, read: Outreach Training Program | OSHA.gov | Occupational Safety and Health Administration
OSHA has an excellent resource for creating a training matrix. You can download OSHA publication # 2254-09R 2015 for more information: Training Requirements in OSHA Standards
Review Existing Policies and Procedures
Safety and health policies and procedures should at least be reviewed annually to determine effectiveness and understanding. This would be a goal for the safety committee.
A review process should be conducted using an audit process. Audits can be performed internally or can be conducted by an outside safety consultant. Either way, an audit of individual policies and procedures helps the organization determine the effectiveness of the current policies and procedures. An audit is a quantitative review and could point out deficiencies that need to be addressed.
An excellent resource for creating and developing audits is found in the OSHA Enforcement tab on the OSHA website: Directives – Directive Number | OSHA.gov | Occupational Safety and Health Administration
Keep in mind that some OSHA regulations require an annual review. For example, the Permit Required Confined Space standard 29 CFR 1910.146: 1910.146(d)(14)
- Review the permit space program, using the canceled permits retained under paragraph (e)(6) of this section within 1 year after each entry and revise the program as necessary, to ensure that employees participating in entry operations are protected from permit space hazards.
Note: Employers may perform a single annual review covering all entries performed during a 12-month period. If no entry is performed during a 12-month period, no review is necessary.
Create an Innovative Approach to Risk Management
Develop a new job safety analysis based on the previous year’s operation. Review the previous job safety analysis from 2024 to identify trends, errors, close calls, or improvements. Have workers give their input.
A quick note. OSHA does not legally require a job safety analysis process (JSA/JHA). Therefore, a job safety analysis is created internally by the company. Input from workers is critical for the job safety analysis to work and be effective.
Consider adding a continuous improvement component to your job safety analysis: debrief. The traditional job safety analysis is designed to incorporate four elements: Name the job to be performed, identify the steps, identify the hazards associated with those steps, and select the most appropriate control to reduce the exposure. By adding the “debrief” element the job safety analysis becomes an important part of the company’s continuous improvement process.
Consult a Professional
Want a second set of eyes? Who doesn’t? Have a safety and health professional assist in the review of the previous year and give some advice on improvement for 2025.
Safety technicians, safety consultants, and certified safety professionals bring a wealth of information to the organization. The Bureau of Labor and Statistics (bls.gov) in their Occupational Handbook states that the Safety Technician occupation is currently experiencing a 14 % growth rate. Read more: Occupational Health and Safety Specialists and Technicians : Occupational Outlook Handbook: : U.S. Bureau of Labor Statistics.
Utilize these professionals!
Preparing the Year End OSHA Injury/Illnesses Forms
This is the time of year to start to review and prepare the OSHA injury and illnesses forms. It’s always time to enhance your safety culture in 2025!
Many employers with more than ten employees are required to keep a record of serious work-related injuries and illnesses. (Certain low-risk industries are exempted.)
Note: The list of partially exempt industries is based on the 2007 NAICS codes. If an industry listed on the “Non-Mandatory Appendix A to Sub part B – Partially Exempt Industries” no longer exists in the 2017 and 2022 NAICS coding system, this would not change your partially exempt status. {See FAQ 2-3 and 2-4}. Minor injuries requiring first aid only do not need to be recorded.
The records must be maintained at the worksite for at least five years. Each February through April, employers must post a summary of the injuries and illnesses recorded the previous year. Also, if requested, copies of the records must be provided to current and former employees, or their representatives.
If company experienced an OSHA recordable injury and/or illness, the following forms must be completed:
- 300 Log of Work-Related Injuries and Illnesses
- 300 A Summary of Work-Related Injuries and Illnesses
- 301 Injury and Illness Incident Report
See the following for more details: OSHA-RK-Forms-Package.pdf
Finally: Happy New Year 2025!
Are you ready to enhance your safety culture this year? Contact us today!