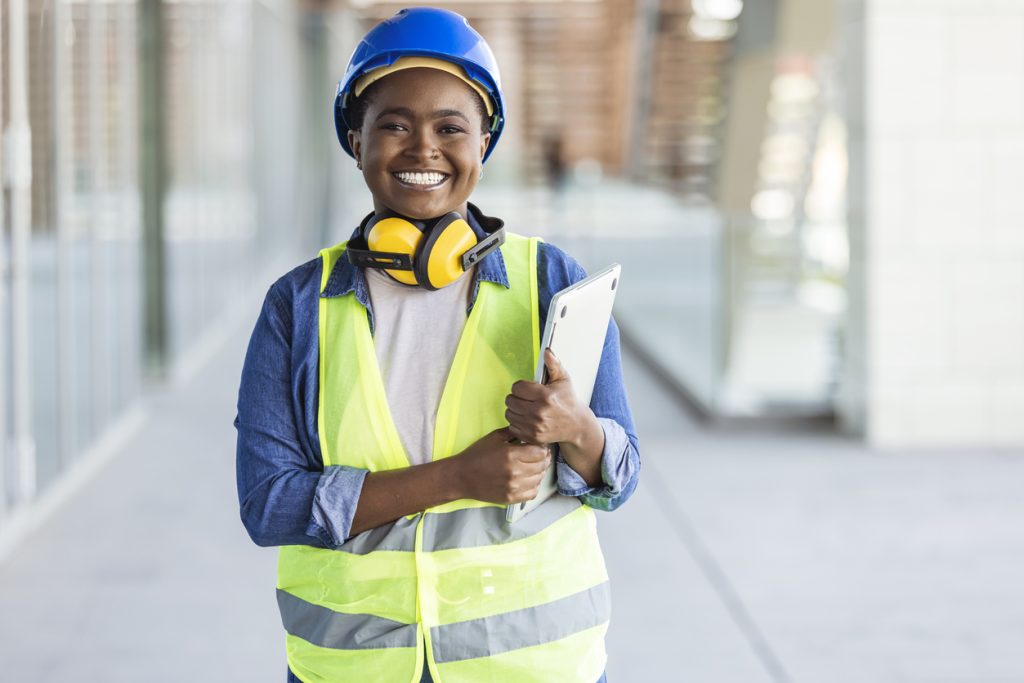
Are you starting or revamping an occupational safety and health program? Well, here is some good advice: The steps are simple, but the process is not easy.
In November of 2016, the Occupational Safety and Health Administration, OSHA, issued an updated Recommended Practices for Safety and Health Programs. The last time OSHA issued recommendations for establishing a safety and health program was 1989.
The new recommendations give employers an excellent blueprint on starting and maintaining an occupational safety and health program.
“The Recommended Practices are designed to be used in a wide variety of small and medium-sized business settings. The Recommended Practices present a step-by-step approach to implementing a safety and health program, built around seven core elements that make up a successful program.”
Source: https://www.osha.gov/safety-management
Here are the seven core steps:
- Management Leadership
- Worker Participation
- Hazard Identification and Assessment
- Hazard Prevention and Control
- Education and Training
- Program Evaluation and Improvement
- Communication and Coordination for Host Employers, Contractors, and Staffing Agencies
Part 3 Starts Here.
6. Program Evaluation and Improvement
It is an old statement: What gets measured gets done. The origin of the statement is up for grabs however the message is clear: when you measure a process/policy/procedure it gives you the information you need to make sure you achieve what you set out to do or fix what you are not.
So, let us clarify for a moment: Program Evaluation and Improvement = A Safety and Health Program Audit.
Once safety and health programs are established, it should be evaluated/audited initially to verify that it is being implemented as intended.
After that, employers should periodically, and at least annually, step back and assess/audit what is working and what is not, and whether the program is on track to achieve its goals.
Whenever these assessments/audits identify opportunities to improve the program, employers, managers, and supervisors—in coordination with workers—should adjust and monitor how well the program performs as a result.
Sharing the results of monitoring and evaluation within the workplace, and celebrating successes, will help drive further improvement.
Program evaluation and improvement/audit includes:
- Establishing, reporting, and tracking goals and targets that indicate whether the program is making progress.
- Evaluating the program initially and periodically thereafter to identify shortcomings and opportunities for improvement.
- Providing ways for workers to participate in program evaluation and improvement.
Action items to accomplish the sixth step:
Action item 1: Monitor performance and progress
Action item 2: Verify the program is implemented and is operating
Action item 3: Correct program shortcomings and identify opportunities to improve
Be aware of bad audits. Never accept an auditor’s recommendations unless the recommendation can be established using a standard or an existing directive as a comparison. Opinions are, well, opinions.
One of the best kept secrets on the OSHA website is the OSHA Directive Library. An OSHA Directive is an internal document that is available to the public but was written as a guide for the OSHA Compliance Officer during an inspection. They can be an excellent source for creating an evaluation/audit.
Here are links to resources the organization should consider accomplishing this step:
OSHA Directives:https://www.osha.gov/enforcement/directives/directivenumber/CPL
Welcome to the Safety Climate – Safety Management Information System (SC-SMIS) https://www.scsmis.com/
7. Communication and Coordination for Host Employers, Contractors, and Staffing Agencies
There must be a system for vetting subcontractors. If not, it can lead to OSHA citations
and expensive legal defenses. Past OSHA cases demonstrate how this can easily
happen if you do not have a process in place to ensure subcontractors have the skills and
experience to get the job done safely. Increasingly general contractors are using
online services to check the safety and OSHA history of subcontractors.
In today’s economy, an increasing number of workers are assigned by staffing agencies to work at specific host worksites under the direction and control of the host employer.
Examples include seasonal workers, such as delivery drivers and warehouse workers, who may be placed in both short- and long-term assignments. In these situations, it is important for the staffing agency and the host employer to communicate and coordinate to provide and maintain a safe work environment for their workers.
In other situations, some workers are employed by a host employer and others by a contractor or subcontractor.
Examples include electrical or mechanical contractors working in a facility, a vendor installing or maintaining equipment, or long-term contractors providing building cleaning and maintenance.
OSHA refers to these as “multi-employer” worksites. In these circumstances, it is important that each employer and contractor consider how its work and safety activities can affect the safety of other employers and workers at the site.
In both temporary worker and multiemployer situations, safety is enhanced if employers establish mechanisms to coordinate their efforts and communicate effectively to afford all workers equal protection against hazards. These mechanisms include measures to ensure that all workers on site (and their representatives) can participate in preventing injuries and illnesses.
Failure to take these steps may undermine safety programs. For example, if the different employers have inconsistent policies for when and where to wear personal protective equipment, workers may mistakenly believe that the equipment is not needed, leading to injury.
Inconsistent safety policies may also cause workers to question the credibility of safety and health programs, resulting in less meaningful employee engagement and participation.
Effective communication and coordination among such employers mean that, before coming on site, contractors and staffing agencies and their workers are aware of:
- The types of hazards that may be present.
- The procedures or measures they need to use to avoid or control their exposure to these hazards.
- How to contact the host employer to report an injury, illness, or incident or if they have a safety concern.
It also means that host employers and their workers are aware of:
- The types of hazards that may arise from the work being done on site by workers employed by contractors or staffing agencies.
- The procedures or measures needed to avoid or control exposure to these hazards.
- How to contact the contract or staffing firm if they have a safety concern.
- What to do in case of an emergency.
Action items to accomplish the seventh step:
Action item 1: Establish effective communication
Action item 2: Establish effective coordination
Here are resources the organization should consider accomplishing this step:
Multi-Employer Policy 1999 https://www.osha.gov/enforcement/directives/cpl-02-00-124
https://www.osha.gov/publications/bytopic/safety-and-health-programs
Temporary Employees: https://www.osha.gov/publications/bytopic/temporary-workers
Temporary Employees: https://www.osha.gov/temporaryworkers
Owners, managers, supervisors, and workers all need to understand the safety and health program’s structure and goals.
Having this knowledge and a plan to implement ensures that everyone can fully participate in the company’s safety and health workplace culture.
End of Simple But Not Easy.