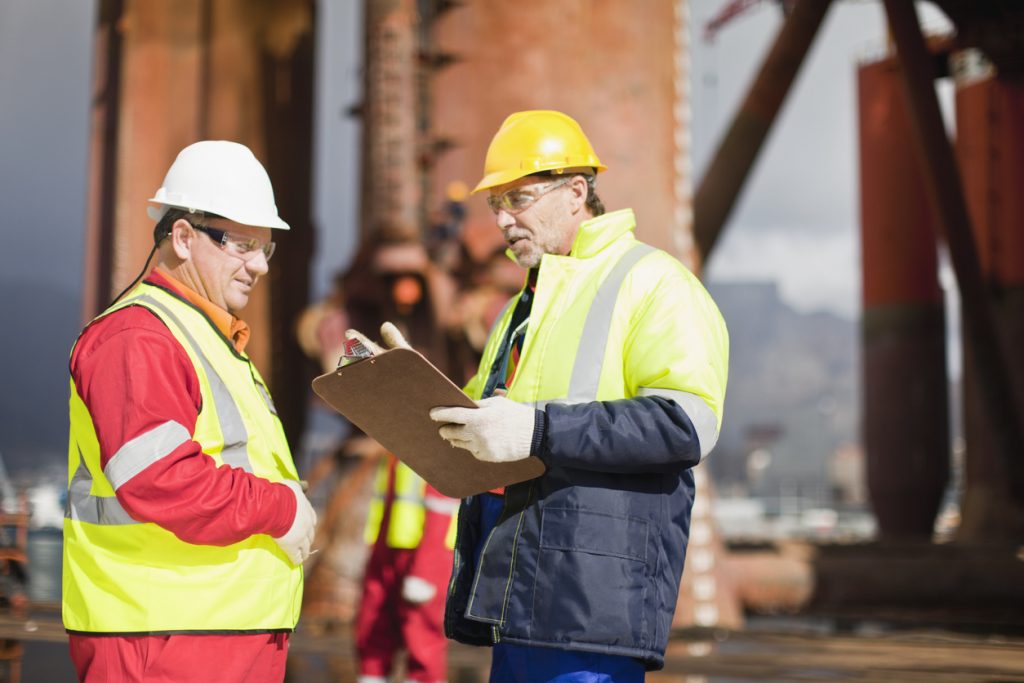
We’ve written about the importance of building and maintaining a Safety Culture more times than I can recall and I would bet that anyone seeing this post agrees that a Safety Culture is mission critical for their business. One of the tools that helps reinforce and encourage the importance of the elements that make up a Safety Culture is the Safety Audit.
Routine but unannounced Safety Audits can really help your staff think and act when they see an unsafe condition or behavior.
This post should encourage you to consider whether you or your business could benefit from effective use of Safety Audits by sharing my top 5, or could also be my bottom 5, findings during unannounced Safety Audits. Deciding upon what order I should put them in was harder than I thought.
No. 5: The dreaded open file drawers.
In spite of our numerous training sessions on trip hazards in the office environment, I received a citation for open file drawers on many of my safety audits. It seems benign to leave the drawer open while you take a few minutes to make copies, but the struggle is real with regard to trip hazards within the office. Don’t make the mistake of ignoring safety hazards in the administrative areas of your work place.
No. 4: Unmarked or mismarked liquid containers.
The mechanical shop was the big offender. Waste oil in unmarked containers, soapy water solutions used for leak detection in mismarked spray bottles and my personal favorite citation – an unidentified liquid believed to be a motor fuel such as diesel in a coke bottle marked as ok for human consumption. It’s hard enough to keep your MSDS files accurate and current without the added creativity of some staff.
No. 3: A dry eye wash station.
In a relatively remote work area with limited access to utilities, someone forgot to return water service to the eye wash station after scheduled maintenance. Of course we audited “right before” they were going to open the valve and test it; just bad timing I guess.
No 2: Improper or inadequate PPE.
While not an excuse, I was always most empathetic to this one where hand protection / gloves was the issue. A craftsman using their hands for work will at times feel they need the dexterity of bare fingers to properly perform the task. Proper procedures and training are critical to aligning Personal Protective Equipment requirements with employee compliance.
No 1: Inadequate or blocked egress.
The most egregious, outrageous, ridiculous safety violation I ever witnessed wins the number 1 spot. A damaged door latch prevented an exterior door to an automotive shop from staying closed. This door was the only egress at the very rear of the shop so it was also the only way out to avoid any fire, fumes or other hazard that may occur in the work area. Being a cold winter week when the door latch was damaged, some innovative soul threaded heavy gauge wire through a hole in the door and adjacent frame to firmly secure the door. Egress from a cloud of fumes or fire would have required long handled metal snips and a clear minded, strong worker to escape.
There have been many unsafe conditions show themselves during the course of routine Safety Audits over the years. The examples described above should never occur where the safety culture is mature.
One tool in your Safety Tool Box is the Safety Audit to identify opportunities to improve your safety culture and help your team to keep safety awareness as the priority it deserves.
The Top Five Safety Audit Findings above are just a few examples of how employees can lose focus on safety. We would love to hear your stories that may help us all improve.